Please
Click A Link Below:
MAKING FLAT GLASS BY THE FLOAT PROCESS
The float process - invented by Sir Alastair Pilkington in 1952, is now
used to make 90% of the worlds window glass. This process allows the manufacture
of clear, tinted and coated glass for buildings, and clear and tinted
glass for vehicles. There are around 260 float plants worldwide with a
combined output of about 800,000 tonnes of glass a week. A float plant,
which operates nonstop for between 11-15 years, makes around 6000 kilometers
of glass a year in thicknesses of 0.4mm to 25mm and in widths up to 3
meters.
A float line can be nearly half a kilometer long. Raw materials enter
at one end. From the other, plates of glass emerge, cut precisely to specification,
at rates as high as 6,000 tonnes a week. In between lie six highly integrated
stages.
Stage 1: Melting and refining
Fine-grained ingredients including Sand, Soda Ash, Limestone, Dolomite
and Salt Cake, closely controlled for quality, are mixed to make a batch,
which flows into the furnace which is heated to 1500°C. Float today
makes glass of near optical quality. Several processes - melting, refining,
homogenising - take place simultaneously in the 2,000 tonnes of molten
glass in the furnace. They occur in separate zones in a complex glass
flow driven by high temperatures. It adds up to a continuous melting process,
lasting as long as 50 hours, that delivers glass at 1,100°C, free
from inclusions and bubbles, smoothly and continuously to the float bath.
The melting process is key to glass quality; and compositions can be modified
to change the properties of the finished product.
Stage 2: Float bath
Glass from the melter flows gently over a refractory spout on to the mirror-like
surface of molten tin,
starting at 1,100°C and leaving the float bath as a solid ribbon at
600°C. The principle of float glass is unchanged from the 1950s. But
the product has changed dramatically: from a single equilibrium
thickness of 6.8mm to a range from sub-millimetre to 25mm; from a ribbon
frequently marred by
inclusions, bubbles and striations to almost optical perfection. Float
delivers what is known as fire
finish, with the luster of new chinaware.
Stage 3: Coating
Coatings that make profound changes in optical properties can be applied
by advanced high temperature technology to the cooling ribbon of glass.
On-line chemical vapor deposition (CVD) of coatings is the most significant
advance in the float process since it was invented. CVD can be used to
lay down a variety of coatings, less than a micron thick, to reflect visible
and infrared wavelengths, for instance. Multiple coatings can be deposited
in the few seconds available as the glass ribbon flows beneath the coaters.
Further development of the CVD process may well replace changes in composition
as the principal way of varying the optical properties of float glass.
Stage 4: Annealing
Despite the tranquillity with which float glass is formed, considerable
stresses are developed in the ribbon as it cools. Too much stress and
the glass will break beneath the cutter. To relieve these stresses the
ribbon undergoes heat-treatment in a long furnace known as a lehr. Temperatures
are closely controlled both along and across the rib.
Stage 5: Inspection
The float process is renowned for making perfectly flat, flaw-free glass.
But to ensure the highest quality, inspection takes place at every stage.
Occasionally a bubble is not removed during refining, a sand grain refuses
to melt, a tremor in the tin puts ripples into the glass ribbon. Automated
on-line inspection does two things. It reveals process faults upstream
that can be corrected. And it enables computers downstream to steer cutters
round flaws. Inspection technology now allows more than 100 million measurements
a second to be made across the ribbon, locating flaws the unaided eye
would be unable to see. The data drives 'intelligent' cutters, further
improving product quality to the customer.
Stage 6: Cutting to order
Diamond wheels trim off selvedge - stressed edges - and cut the ribbon
to size dictated by computer. Float glass is sold by the square meter.
Computers translate customers' requirements into patterns of cuts designed
to minimise wastage.
Click to return
to technical index
The Rolled Glass Process
The rolling process is used for the manufacture of patterned flat glass
and wired glass. A continuous stream of molten glass is poured between
water-cooled rollers.
Patterned glass is made in a single pass process in which glass flows
to the rollers at a temperature of about 1050ºC. The bottom cast
iron or stainless steel roller is engraved with the negative of the pattern;
the top roller is smooth. Thickness is controlled by adjustment of the
gap between the rollers. The ribbon leaves the rollers at about 850ºC
and is supported over a series of water-cooled steel rollers to the annealing
lehr. After annealing the glass is cut to size.
Wired glass is made in a double pass process. The process uses two independently
driven pairs of water cooled forming rollers each fed with a separate
flow of molten glass from a common melting furnace. The first pair of
rollers produces a continuous ribbon of glass, half the thickness of the
end product. This is overlaid with a wire mesh. A second feed of glass,
to give a ribbon the same thickness as the first, is then added and, with
the wire mesh "sandwiched", the ribbon passes through the second
pair of rollers, which form the final ribbon of wired glass. After annealing,
the ribbon is cut by special cutting and snapping arrangements.
Window Energy Rating (WER)
Window Energy Rating was formally introduced to Part L of the Building Regulations in 2006 as a method of compliance for domestic replacement windows. It introduced the concept of giving an overall energy rating from A (Best) to G (Worst). The British Fenestration Rating Council (BFRC) operates the UK's national system for rating the energy efficiency of windows. Once tested, fabricators are able to sell their windows with enegry efficiency labels similar to below:

To date a pass of documanet L - as outlined below, requires an E rating. However, there are revisions to Document L due for publication in April 2010 which are set to be adopted as required practice in October 2010. These revisions are rumoured to require a C rating as a pass.
Leicester Glass already has the ability to produce D G Units which have been tested to an A rating when coupled to Season Master's Synseal Shield windows. We believe that this is what the market will demand and expect. Whilst awaiting conformation of the new requirements, we are looking very closely into all the options so that we will be best placed to offer our clients C to A rated components and windows to the highest specification, most economically.
The Government's Approved Document L -
How it's going to effect Us and You.
You may well have read in the trade press that our industry has had further
restrictions placed upon it by the British Government. Our industry was
awash with rumors as to what the new regulations may mean. Below are our
interpretations of the thinking behind the changes, the regulations themselves
and how you and we are affected.
Brief History
Our Government has made it one of their key goals to reduce Carbon emissions
significantly by the year 2010. They set up committees to investigate
all possible ways of saving on fuel which will reduce our national Carbon
output. One area they have targeted is heat loss from houses and commercial
buildings. A direct result of this was the publication, on 31st October
2001, of the Government's Approved Document L which became law in April
2002. In two parts, ADL1 (referring to domestic properties) and ADL2 (all
other types of building) extend Building Regulations to cover replacement
window installations from April 2002.
The Regulations
Document L requires the installer to consider heat loss when fitting,
new and replacement, whole window / door assemblies. All materials used
in the window or door are given 'U' values, which correspond to their
heat transfer levels. Basically, the lower the 'U' value the better the
heat saving and therefore carbon saving.
The new regulations include complicated calculation methods to work out
'U' values. To keep it simple for us in the glass trade, the window and
door industry generally need to concentrate on attaining a 'U' value of
no higher than 2.0 for Wood & UPVC and 2.2 for Metal.
There are to be some important areas of exemption in the first phase
of implementation:
Only complete frame assemblies will initially be covered by the regulations.
Replacement of broken panes of glass can be completed on a 'like for like'
(or better) basis.
Conservatories are not included in the regulations providing they do
not have heating and are separated from the main building i.e.. Have dividing
doors.
Trickle ventilation and some other items of furniture, such as cat-flaps
are exempt.
Shops, historic buildings and buildings in conservation areas are also
exempt.
The regulations became law on April 1st 2002. The Glass and Glazing Federation
negotiated an extension until July 1st 2002 for work already commissioned
before April 1st. After these dates, an installer must by law comply with
all parts of Document L.
Compliance will be scrutinised by the Local Authority Building Control
Departments. Any installer must gain Local Authority approval to carry
out an installation. Building Control Departments will need to be assured
that the relevant U values have been achieved.
The Glass and Glazing Federation, with others, run a scheme of self-certification.
Under the name of FENSA this scheme offers registration with Local Authority
Building Control and so very significantly lower the cost of compliance.
However, to be a member of the scheme any installer has to show, among
other things:
Sufficient Insurance cover for himself and third party liability
Comprehensive Health and Safety documentation
Comprehensive training records
Installers of complete, new or replacement, frames must register or go
though the local authority for each contract. The penalty for any installation
shown not to comply is set to be in the region of £3,000 per installation
with an addition of £50 per day until conformity is achieved.
Leicester Glass Company Limited are a FENSA registered company.
The Implications
In real terms, the regulations mean that new installations have to be
much more heat efficient than the average installation at present. No
ordinary 4mm unit fitted into any system will comply directly with the
new regulations (though there are exceptions to this). The easiest way
to achieve the new U values, will be to use double glazed sealed units
with be a minimum of one pane float glass, one
pane Pilkington K, with a spacer of at least 12mm and these must be
Kite Marked as a quality assurance guarantee.
The Law and Us
Leicester Glass is primarily a supplier of materials to the Fenestration
market. For some time we have been manufacturing sealed units with the
option of Pilkington K. We have installed new Pilkington K washing facilities
to aid our handling of this notoriously 'awkward to handle' glass type.
In addition Leicester Glass Company Limited has invested considerable
time and money attaining a British Standard Kite Mark.
For the 'glass only' replacement markets Leicester Glass Company Limited
continues to offer single glazed panes and double-glazed sealed units
with smaller cavities than 12mm and with or without Pilkington K. However
we will be happy to advise clients to prevent them falling short of the
new regulations.
In association with Season Master Windows Limited we will continue to
supply UPVC frames. Our systems extruder, Synseal, have assured us that
their products when used with sealed units incorporating Pilkington K
will comply with Document L. Secondary glazing to an existing frame is
exempt from Document L and offers a way of lowering U values to existing
windows.
We were one of the 'first phase' of companies to gain a FENSA registration.
As suppliers of materials we need to be able to assure clients only
that our products comply. Leicester Glass either glaze to existing frames
(which are exempt) or act as Subcontractors for new windows fitted by
others. It will remain the responsibility of the primary contractor to
acquire the necessary permission.
Document L is an important change to our industry.
Leicester Glass Company Limited sees this as an opportunity to widen the
gap between ourselves and our competitors. It is important to be clear
how the regulations will affect your business.
If we can supply any further information please email
or contact us.
Click to
return to technical index
Safety Glazing Considerations - The Governments
Approved Document N.
The Legislation
In 1981 BS 6206: 'Specification for Impact
Performance Requirements for Flat Safety Glass and Safety Plastics for
use in Buildings' was published. This outlined the criteria by which safety
glazing materials are now measured.
Critical areas requiring safety glazing were
first published as part of The Building Regulations England and Wales
1991 Part N 'Glazing - materials and protection'. This brought together
safety glass, as defined in BS 6206 with key areas of building which require
such glass. The Building Regulations are only concerned with glazing which
forms part of building structures.
BS 6262: ' Code of practice for glazing buildings'
Part 4: 1994 'Safety related to human impact' extended the cover of safety
glazing beyond building structures. It set standards for other locations,
in addition, such as shower screens, shower cubicles, mirror glazing for
cupboards and wardrobes.
Safety Glass Options.
BS 6206 details impact tests utilising lead
shot-filled leather bags weighing 45kg, dropped like a pendulum from different
heights.
There are three safety glazing classifications:
A (the highest), B, and C (the lowest).
Toughened Glass:
All the toughened glass Leicester Glass Company Limited offer has a Class
A classification.
Laminated Safety Glass: We
offer three types of laminate products: PVB (poyvinylbutyral), CIP (cast-in-place)
and Polyester resin interlayered. These normally achieve at least a Class
B classification dependent on glass and interlayer thickness.
Wired Glass:
'Safety wired' typically have thicker wires implanted within their structure
or a CIP laminate interlayer and obtain a Class C classification.
Polycarbonate: Leicester
Glass Company Limited only offer Lexan which is the brand name of the
Polycarbonate manufactured by General Electrics. It carries a Class A
Classification.
Glasses meeting the requirements and intended
for use as safety glasses must be permanently marked as conforming to
BS 6202.
Critical Locations.
The regulations specify areas of glazing
which the authorities deem to be 'Critical'. These locations are depicted
below:
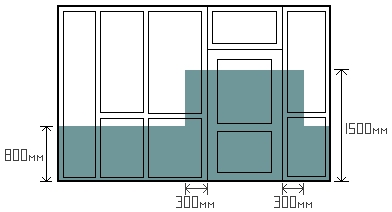
The following locations should be regarded
as critical and thus should be glazed only with a safety glass to BS 6206:
a) Between finished floor level and 800mm
above it.
b) Between finished floor level and 1500mm
above if in doors or side panels within 300mm of the edge of a door.
Exceptions
a) An aperture with a smaller dimension
being less that 250mm and of total area less that 0.5sq/mt may be glazed
with a glass of minimum (nominal) thickness of 6mm which does not comply
with BS 6206.
b) An aperture forming parts of fronts
to shops, showrooms, offices, factories and public buildings, which are
supported on all edges, may be glazed with a glass of equivalent robustness
but which does not comply with BS 6206. Thus:
8mm must not exceed 1100 x 1100mm, 10mm
must not exceed 2250 x 2250mm, 12mm must not exceed 3000 x 4500mm, 15mm
and thicker has no limit.
c) Panes protected by a suitable barrier.
Click
to return to technical index
Insulating Glass Unit
testing to meet European standard
The impending ratification of the outstanding parts of EN 1279 'Glass
In Building - Insulated Glass Units' will allow manufacturers to demonstrate
compliance with the Construction Products Directive (CPD) and achieve
CE Marking of Insulating Glass Units (IGUs).
CE Marking is the easiest way to demonstrate compliance and will be a
requirement for many EU countries. Although the UK does not currently
require CE Marking, compliance with the CPD will be mandatory and IGUs
will need to have passed EN 1279 to fulfil the requirements.
Currently in the UK there is no legislative requirement to test IGUs,
although almost invariably buyers will expect a demonstration of performance,
traditionally through BS 5713 -Specification for hermetically sealed flat
double glazing units. BS 5713 will ultimately be superseded by EN 1279,
which is already being tested against and is perceived to be a more onerous
method of proving IGU performance.
The six-part standard refers to factory quality management, CE Marking
requirements, production and component tolerances as well as test evidence.
Testing is designed to prove the performance of the sealed unit under
an accelerated ageing regime of temperature, moisture and light conditions
to represent service life. It considers moisture penetration and emission
of volatile gases against accepted levels of performance in relation to
minimising condensation or fogging within the unit.
Leicester Glass has, for some years, held a Kitemark licence with
The British Standards Institute (BSI). We have had our units tested
and we hold certification from BSI confirming that they passed the more
stringent EN 1279 requirements.
Click to return to technical index
119-125 Bridge Road, Leicester
LE5 3QP T: 0800 1694357 F:
0116 2460462 E:
enquiries@leicesterglass.co.uk
|